The North American Wave Engine Corporation, a developer of affordable next-gen propulsion technology and aerial systems, has demonstrated complete flight capability on a UAV using a jet engine that requires no moving parts. A demonstration flight included self-powered take-off, climb-cruise and landing.
The propulsion system is generally the most expensive and complex component of a jet powered aircraft, and this technological development signals major improvements for the cost and rapid-producibility of future jet powered aircraft.
Wave engines* are a class of aircraft engines that operate using pressure waves instead of rotating machinery. Intermittent combustion inside a hollow tube produces pressure waves that push hot gases and produce thrust. Wave Engine Corp.’s proprietary technology enables high speeds and allows for an order-of-magnitude reduction in the cost and complexity of jet propulsion, which is a critical enabler for an increasing number of applications that call for affordable and rapidly-producible jet propulsion systems and aircraft.
For the demonstration flight, a 50+ lbf (222+ N) thrust wave engine was used as the sole powerplant on a 100 lbs (45 kg) gross weight Conventional Take-Off and Landing UAV. Remote instant start on liquid fuel was also demonstrated as part of the flight sequence.
The company has developed engines ranging from 50 lbf (222 N) to 250 lbf (1112 N) maximum thrust suitable for aircraft ranging from 100 lbs (45 kg) to 1000 lbs (450 kg) gross weight, and demonstrated operation on gasoline/petrol (87 Octane), kerosene-based fuel (Jet-A/JP-8) and sustainable ethanol-based biofuel (E85).
The company also announced that it had successfully demonstrated multiple mid-air starts and operated its engines at airspeeds up to 200 mph, limited only by the practical limits of the test facility.
Additionally, the company has demonstrated Thrust Specific Fuel Consumption (TSFC) levels under 2.0 lbs/lbf-hr to rival the efficiency of turbine-based engines, and performance continues to improve as development progresses.
“We continue to push the performance and flight envelope,” said Daanish Maqbool, CEO of Wave Engine Corporation. “We have worked for years to harness the power of sound and fire, and we believe it is going to change the industry.”
The company also announced its launch product, the 50+ lbf thrust J-1 engine, and welcomed potential partners for inquiries and demonstrations.
While you can read more here about how pulsejets work, as Wave Engine describes, a simple explanation is that they “operate using pressure waves instead of rotating machinery. Intermittent combustion inside a hollow tube produces pressure waves that push hot gases and produce thrust.”
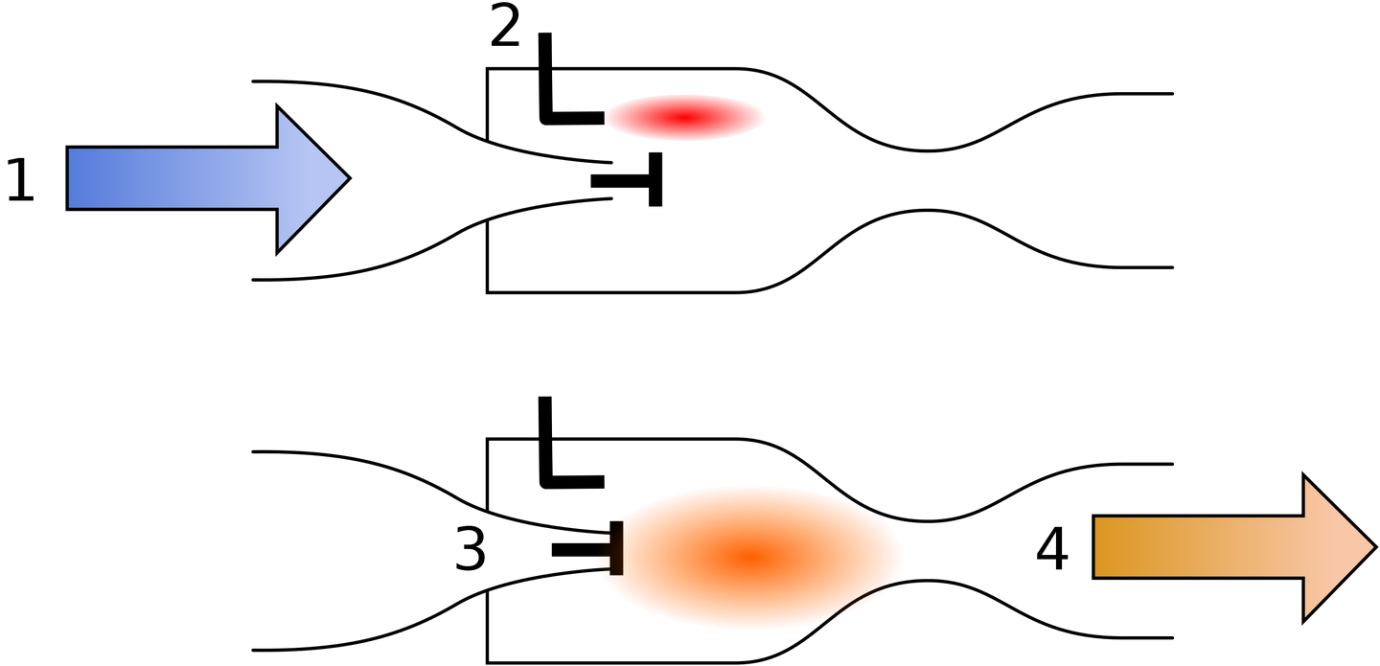
Pulse jet schematic. First part of the cycle: (1) air intake, mixed with fuel (2). Second part: the valve (3) closes and the ignited fuel-air mix propels the craft. Cyrille Dunant/Gregor Shapiro/Wikimedia Commons
The high speeds offered by pulsejets are also a factor in their favor, especially when compared to the propeller-based powerplants otherwise frequently found on many smaller military drones.
While pulsejet designs have been around for a century, the technology has been largely dismissed by the commercial aviation industry for being too loud and difficult to regulate during flight. They are used in model aircraft, drones and industrial applications. Pulsejet designs have been tried on experimental helicopters, and there is the belief, as Wave Engine Corp. shares, that the pulse detonation engine (PDE) promises higher efficiency than turbofan jet engines.
Boeing has a proprietary pulsejet engine technology called Pulse Ejector Thrust Augmentor (PETA), while aircraft engine makers Pratt & Whitney and General Electric have PDE research programs that use pulsejet engines for testing concepts early in the design phase. Boeing may use it on its Light Aerial Multi-Purpose Vehicle (LAMV) for future combat scenarios.
Wave Engine first tested the technology in 2020 by mounting a prototype engine on a piloted glider and turning it on in mid-flight. The latest unmanned flight had the engine integrated into the UAV. Of course, going from a 100-pound prototype to a commercial jet is a big leap. It will involve years of testing, development and certification for the technology to be proven, as well as getting aircraft manufacturers to design its jets around the engine.
About Wave Engine CorporationBased in Baltimore, MD, Wave Engine Corp. is a focused group of scientists, engineers and former Fortune 500 executives that is leveraging recent technological developments in propulsion, acoustics and combustion control to develop the next generation of propulsion and aircraft systems. With its unique set of technical experts, test facilities and intellectual property, Wave Engine Corp. is committed to leadership in technology and product development for an emerging breed of jet propulsion and aircraft systems.*The wave engine is a contemporary variation of the pulsejet engine, which was first used on German V-1 guided missiles in WWII.
Sources: Press Release; Robb Report; The Warzone