Since their initial conception in the early 20th century, Flexible Printed Circuits, (FPCs) have found their way into a wide variety of industrial and consumer electronic products. Until recently, applications have been limited by FPCs’ relatively short length, with very few companies capable of making them longer than a couple of metres.
However, a new FPC manufacturing process, Improved Harness Technology™ (IHT), patented by UK company, Trackwise, has changed the dynamics of FPC manufacturing, enabling the creation of limitless length, multilayer FPCs.
Unmanned Aircraft Systems, (UAS), is one of many sectors which can expect to benefit from a whole landscape of new applications which will be unlocked by this innovative manufacturing process.
A Brief Overview of FPCs
First described by German scientist and inventor Albert Hanson in his early 20th-century patents as multiple layers of foil conductors laminated onto an insulating board, FPCs now represent a multi-billion-dollar global market. Like their rigid equivalents, FPCs are produced via a subtractive process by chemically etching copper away from its substrate to reveal the conductive circuit elements beneath. Substrates can be manufactured from a range of materials, the most common being polyimides and polyesters, with other advanced polymers emerging, including thermoplastic varieties, which can function at extremely high temperatures.
FPCs are manufactured in a number of different configurations, including single or double-sided, with multi-layered FPCs available for higher density interconnects. Multilayer FPCs, (figure 1), are formed by bonding together a number of single or double-sided flexible circuits and plating through to create a compound interconnected device.
FPCs are further categorised by their application type – either dynamic or static. In a static application, the flexibility is required only at installation, e.g. to fit inside a confined or aerodynamic space whereas, in a dynamic application, the FPC may be flexed many times during its life, such as in a printer cable or a car door hinge.
FPCs offer multiple benefits to the system designer, (Table 1), primarily space and weight savings along with reduced manufacturing costs and improved circuit performance. FPCs also have the ability, after further processing, to serve as a final circuit assembly and their 3D characteristics enable them to be folded and shaped into precise form factors, (figure 2), in a way that’s virtually impossible to do with traditional PCBs and cables.
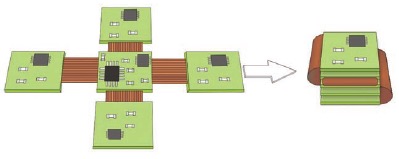
Figure 2: FPCs 3D characteristics enable them to be folded and shaped into precise form factors (Source: Flexible Circuit Technology, Fourth Edition, Joseph Fjelstad)
The automotive aerospace and military sectors are particularly heavy users of FPCs but, given their many benefits, it’s not surprising that FPCs are also found in a wide variety of electrical and electronic products, including smartphones, laptops, cameras and games consoles as well as wearable devices for sports and medical applications from automotive, IT and industrial equipment to consumer, medical and entertainment.
Benefit |
Description |
Space saving |
Ultra-thin dielectric substrates, some as thin as 25µm or less, together with their planarity, have made it possible to bond circuits to, or within, the structure of a given product |
Weight saving |
Subsequent weight reduction is amplified as less fixings and connectors are required. Likewise, reduced copper content and smaller conductors make a further impact |
Versatility |
FPCs are custom-made to bend, fold and fit into almost any shaped housing |
Ruggedness |
FPCs demonstrate robust connections compared to wire harnesses as their flat foil conductors dissipate heat more efficiently, as well as carrying more current than their round wire equivalents. Fewer interface connections enhance reliability; plus, physically they’re more resistant to vibration and shock than rigid PCBs |
Higher operating temperature |
Improved thermal stability, notably with polyimide materials, enabling the circuit to tolerate more extremes of heat than rigid PCBs; reduced thermal mismatch |
Crosstalk and noise |
More easily controlled using a uniform conductor pattern within the flexible circuit. Ground plane options comprise solid copper, aluminium, lightweight cross-hatched or lightweight shielding films |
Effective EMC performance |
Lowered radiated emissions due to smaller ground loop, produced by the guard traces; and improved differential-mode transmission loss features |
Data bus applications |
Improved control of impedance characteristics, lowered transmissions loss and reduced radiated field emissions due to shorter current return paths |
Simple, reliable installation |
Rapid assembly with less component parts; better repeatability with less manual intervention, without the need to colour-code wiring. Results in reduced installation costs, lower risk of rejects during assembly and less in-service failures |
Table 1: FPCs offer multiple benefits to the systems designer
IHT Manufacturing Process Enables Limitless Length FPCs
Whilst traditional FPC manufacturing processes have limited their length to 610mm, (although a few manufacturers have been capable of producing circuits a few metres long), the new IHT manufacturing process, overcomes these constraints. IHT uses machine-intensive and dynamic, roll-to-roll processes, as opposed to the traditional static ones, to enable the cost-effective manufacture of multilayer FPCs of any length.
The automotive, telecommunications and aerospace industries are among the initial sectors benefitting from IHT production techniques with applications which previously required heavy and bulky wire harnesses being transformed by FPCs. In aerospace, for example, extended-length FPCs are replacing complex, large and heavy wire harnesses, enabling the space and weight restrictions of an increasing number of in-cabin and on-board systems to be met.
FPCs and UAVs
UAV projects are particularly set to benefit from the design and manufacture of unlimited length FPCs. With demonstrated weight savings over traditional wire harnesses of up to 75%, FPCs have obvious benefits for energy efficiency and payload considerations. Additionally, FPCs’ ability to function as a subsystem enables the integration of distributed electronics such as sensing and signal conditioning functionality, effectively creating a smart interconnect, supporting a high sensor and/or instrument density within the UAV.
For smaller vehicles, sensor density is further supported by the 3D characteristics of FPCs, enabling innovative layouts to be incorporated into small spaces. In an example of how larger UAVs can benefit from the capabilities of FPCs, Trackwise recently supplied a 26m-long shielded FPC to a UAV manufacturer, intended for transferring power and signals across the wingspan of their vehicle. Based on a polyimide substrate, the planar structure of the FPC dissipates heat better than conventional wiring, enabling higher current carrying capacity for a given weight of copper conductor.
On this project an estimated 60% weight savings were achieved over traditional wire harness by using FPCs for the entirety of the UAV interconnect system, resulting in a higher payload and/or improved speed and range for the vehicle. The vehicle’s assembly time and cost was also reduced as a result of the characteristics of FPC manufacturing, including circuit consistency, fewer connection points, leading to higher reliability and easier installation.
Conclusion
The ability to manufacture FPCs of unlimited length promises to enable a new generation of applications, particularly in the aerospace and automotive sectors where sustainability and environmental protection are critical factors. Extended length FPCs have already been shipped for a number of UAV projects and have generated significant weight saving and cost benefits. The inherent characteristics of FPCs are well suited to the environmental and electromagnetic conditions which may be experienced by UAVs and the break-through IHT manufacturing process promises to deliver a number of exciting future projects.